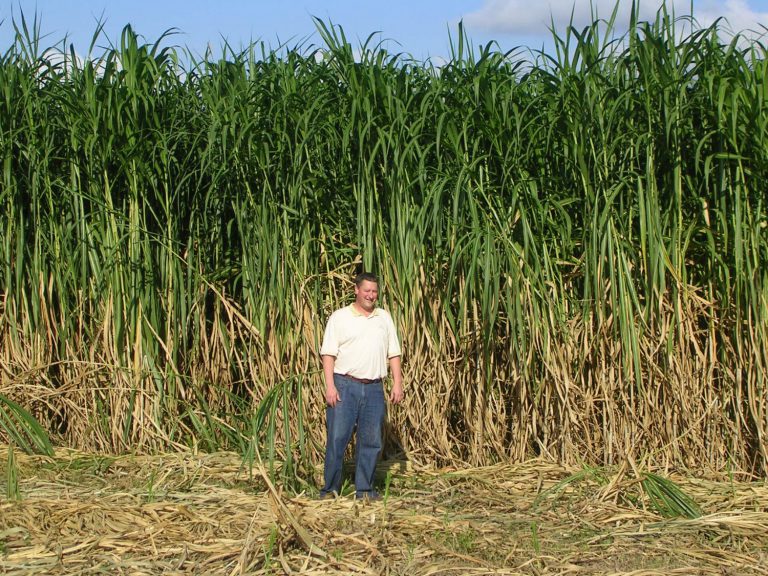
Harvesting for Biomass Below the Border
May 2015
The biomass industry in Central and South America is reaching monumental heights – literally – and it looks to rise even higher.
The traditional harvesting method in these regions has been to harvest sugarcane stalk, crush it for the juice and make ethanol and sugar. The remaining material – bagasse – is then burned in boilers at the sugar mill to generate steam and electricity to power the plant, making these operations self-sufficient.
Starting in 2015, it will be illegal to burn the sugarcane leaves before harvesting the cane stalk, which means the harvest process will include harvesting the leaves as well. Rather than seeing this as an obstacle, operations are instead viewing it as an opportunity to generate more electricity. Mills will now use both bagasse and leaves to fuel the boilers, in the process creating excess energy which local governments are paying to have placed on municipal grids.
The new source of revenue has prompted many sugar mills to expand production of electricity. In addition to using the bagasse and sugarcane, they are now growing and harvesting energy grasses (which share many qualities of sugarcane and reach towering heights) in order to make even more electricity.
Arundo Donax – a hollow, bamboo-like grass – can stretch upwards of 14-15 feet, outstanding by all standards of grass, and yet that’s a short feat compared to King Grass, which can grow as high as 20 feet. Indeed, this isn’t you lazy neighbor’s overgrown lawn.
These energy grasses not only grow extremely tall – they grow quickly.
“It’s incredible how it grows,” said Jay Van Roekel, Biomass Business Unit Manager at Vermeer, who makes regular trips to the region.
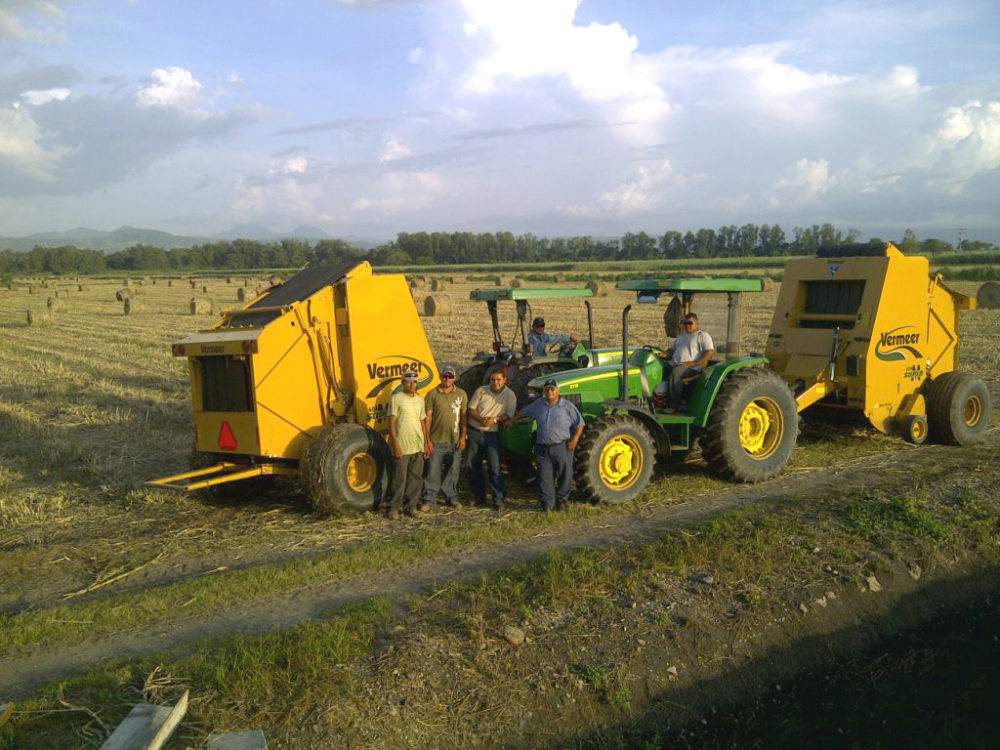
Quick growth rates paired with extended growing seasons in the tropical climate (nine months a year) mean growers can harvest these towering energy grasses three or four times annually.
Arundo Donax makes an exceptional biomass crop because of its propensity to release moisture quickly because it is hollow.
“You can mow it down and bale it the next day below 30 percent moisture. It’s like you cut it and the water just runs out the bottom of it,” said Van Roekel. “It’s an amazing crop because you can bale it dry and stably store it, even in the tropical climate.”
Of course when you’re mowing down grass that’s nearly two stories tall, any old push mower won’t do. King Grass, according to Van Roekel, is an even greater challenge because it’s a corn-like crop that is incredibly fibrous and doesn’t release moisture with the expediency of Arundo Donax.
“It’s a challenge because it’s full of water. To get it to dry down is tough,” said Van Roekel. “But we’ve been getting good results with Vermeer mower conditioners. It’s a lot of material to pull through a mower. But we’re mowing it down and we’re able to bale it.”
Van Roekel said the size, performance capabilities and durability of the Vermeer 604 Super M baler makes it a good choice for operators looking to conquer the formidable energy grasses. The 4-foot wide bales produced by the 604 Super M are especially important in Central America. The variable chamber allows the customers to create bales that are the proper weight and size for their loaders and trucks to transport.
“We get too spoiled (in North America) with loaders on the front of the tractors that you can throw a spear on,” said Van Roekel. “Bale handling is a challenge in many areas (of Central and South America). You can find a tractor to run a baler or rake, but then you have a bale sitting there and what do you do? You can’t roll it off. You have to mechanically move it. I have seen backhoes, pay loaders, and sugarcane loading devices used to handle bales, just about everything but front-end loaders. So there is a great opportunity to improve bale handling in these developing regions.”
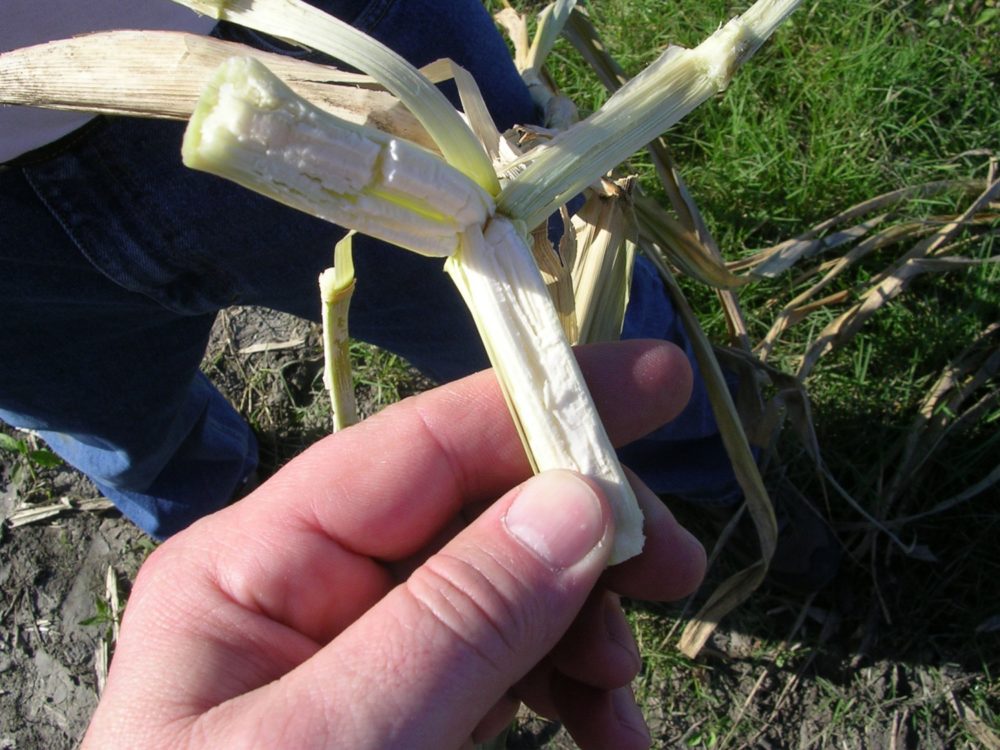
Van Roekel said one popular method of transport is to use 8-foot-wide wagons, which can handle two 4-foot-wide bales side by side. The demand for 4-foot-wide bales has made the 604 Super M baler, 504 PRO baler and 404 PRO baler popular in these regions.
Many operators then use Vermeer tub or horizontal grinders to break down the bales. This material is then burned in the boilers to make steam and eventually electricity. The process is proving to be more efficient and economical than traditional methods that utilized fuel oil.
“With gas and oil price volatility, [mill operators] determined that it’s better to have their own reliable energy source,” said Van Roekel. “One operation has seen a 50-percent reduction in energy costs after one year, by doing it themselves. They don’t’ have the volatile market when it comes to purchasing fuel oil and they’re a little more self-supportive.”